It’s common to have many different people involved during large construction projects. You have specialized sub-contractors, designers and other professionals who need to work together.
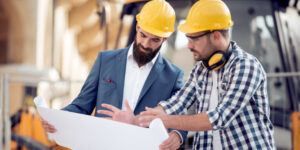
A General Contractor is the person who oversees all of these people and their work to ensure that everything stays on schedule. They also provide a point of contact between all parties. Visit https://www.infinity-construct.com/ to learn more.
Project management is the overall coordination of a construction project from its initial concept through to completion. In contrast to a general contractor, who is primarily responsible for the physical construction of a project, a construction project manager is involved in the high-level coordination of the project to ensure that the client’s goals are met, the project stays on budget and remains within schedule.
Project managers work closely with a variety of parties to coordinate and oversee the project’s construction including the architect or designer, engineering firm, client, general contractors and subcontractors. They are also responsible for assembling the team that will complete the project by issuing a request for proposals to architectural, engineering and general contracting firms and selecting those that best fit the client’s wishes and project outline.
They are also responsible for obtaining all required building permits and securing the property, providing temporary utilities on site, managing personnel, disposing or recycling construction waste and monitoring the progress of the project against schedule and budget. The construction project manager will also be a liaison between the client and various specialty contractors to ensure that all issues are addressed in a timely manner.
Unlike a general contractor who works for a percentage of the total project cost, a project manager works for a flat fee or hourly rate. They are a great option for homeowners who want to remain hands-off during their remodel. Like a personal assistant, they will handle all the minutiae of your project and ask for little input from you. They will pitch ideas, but ultimately the decisions are yours. Oftentimes, they’ll stay on site throughout the project as well to keep things running smoothly.
Sub-Contractors
General contractors often rely on sub-contractors to complete certain aspects of large projects. For example, they may hire a concrete contractor to pour the foundation for a skyscraper while another company might install the windows and bricks. This helps the GC stay on schedule and keep workflow moving. Subcontractors are also important to a GC because they provide a wide range of skills and expertise. For this reason, it is critical for a GC to do their homework and find the best ones. They will typically request information on a potential subcontractor’s safety record, finances, bonding capabilities, litigation history, insurance coverage, relevant work history and experience.
Many GCs work on a negotiated contract basis with project owners. In this scenario, the GC will review the drawings and scope of work and then obtain quotes from qualified specialized subcontractors. The GC then adds their own overhead costs to come up with an overall price for the job and then agrees to perform the work at that price. This method saves time and money on the bidding process and allows the GC to build in some profit margin.
Some states require that GCs be licensed, which gives their clientele a sense of confidence in their abilities. Getting licensed also helps a GC establish credibility and trustworthiness in the construction industry. In addition, it gives them the ability to protect their lien rights in case they do not get paid for their services.
A GC must be skilled, trustworthy and professional to meet the challenges of their role. They are responsible for resolving issues on the construction site and maintaining discipline among all parties. They are also in charge of ensuring that all the materials used on the project are high quality and durable. This is because the quality of the materials can affect maintenance costs after the premise is constructed.
Scheduling
A general contractor oversees all the work on a construction project and manages all the different professionals working on it. They have to meet deadlines and ensure that all the different processes are running smoothly. They must also be able to adapt and deal with any challenges that arise on the project. This is why it is important for a general contractor to have experience and the necessary licenses.
The work of a GC is not done in isolation, and they must work with the project architect to ensure that the construction takes place according to the design and blueprints. This includes planning, cost estimation, and determining the necessary materials and manpower to be deployed on the site. The GC also coordinates with the sub-contractors and ensures that all the work is done correctly before payments are disbursed to anyone involved in the construction process.
Large construction projects require the movement of a lot of raw materials and building components. This requires a team of professionals with experience in supply chain management. The GC will assign this team to handle vendor sourcing, estimates, capacities, quality work, turnaround times, and invoice processing.
While many property owners might think that a GC is expensive, it’s important to remember that they will save you time and money in the long run. They will also be able to get your project done on time and within budget.
Whether you’re building a new home or remodelling an existing one, finding the right contractor is crucial. Make sure they have a valid license and insurance coverage, and ask about their previous projects. It’s also a good idea to check out the Better Business Bureau to see if they have any complaints against them.
Budgeting
A construction budget is a tool used by general contractors to anticipate and plan for all costs associated with building a project. It is usually created with the help of professional estimators and quotes from suppliers and subcontractors. The budget is broken down into two categories: hard and soft costs. Hard costs include the cost of all materials and equipment that go into a construction project, such as nails, wood, metal, drywall, paint, mechanical and electrical equipment, and lifting machinery. Soft costs, on the other hand, are all non-material expenses, such as supervision labor, temporary utilities, trailer rental and project management fees.
To develop a construction budget, general contractors first perform a take-off of the job. This involves looking at the plans and specifications to determine exactly what work is needed, and how much of it there is. Afterwards, they assign a budget line item for each scope of work or trade that is required. For example, a small office remodel may require demolition services, metal framing, drywall, painting, doors and hardware, and mechanical and electrical work.
General contractors also create a contingency budget for unexpected costs that might arise during the construction process. These expenses are typically carried by either the general contractor or the client, depending on the contract type. It is important to monitor actual expenses compared to the budgeted costs so that you can identify any deviations and take corrective actions.
Quality Control
General contractors must make quality control a priority on every project they undertake. This is because the quality of a project has an impact on all parties involved. A poor quality project will increase the risk of cost overruns and delays. This can hurt a construction company’s bottom line and hamper their ability to remain profitable quarter-to-quarter. To avoid these problems, GCs must ensure that they are using qualified sub-contractors for their projects and making sure that they are following strict timelines for completion.
The main goal of quality control is to ensure that all work is done correctly and meets the design specifications. Identifying issues and addressing them promptly is crucial to prevent delays and additional costs. For example, if an architectural or structural element is not in alignment with the design specifications, it should be immediately addressed. This could mean repositioning or reinforcing the component, or it may require a complete redesign of that particular part of the facility. In either case, this should be a collaborative effort between the general contractor and the design team.
A general contractor’s Quality Control (QC) process typically involves two elements: a QC plan and QC procedures. The QC plan defines how the contractor intends to manage project quality requirements and the QC procedures define how this is actually accomplished on the jobsite.
Some QC practices involve the inspection of completed work and of batches of materials to insure that they meet minimum standards established in the project specifications. The inspections are often conducted by the QA department or independent inspectors. QC procedures also include review of supplier records, testing supplies to verify that they comply with existing quality assurance specifications, and auditing suppliers who are not currently working on the current project.